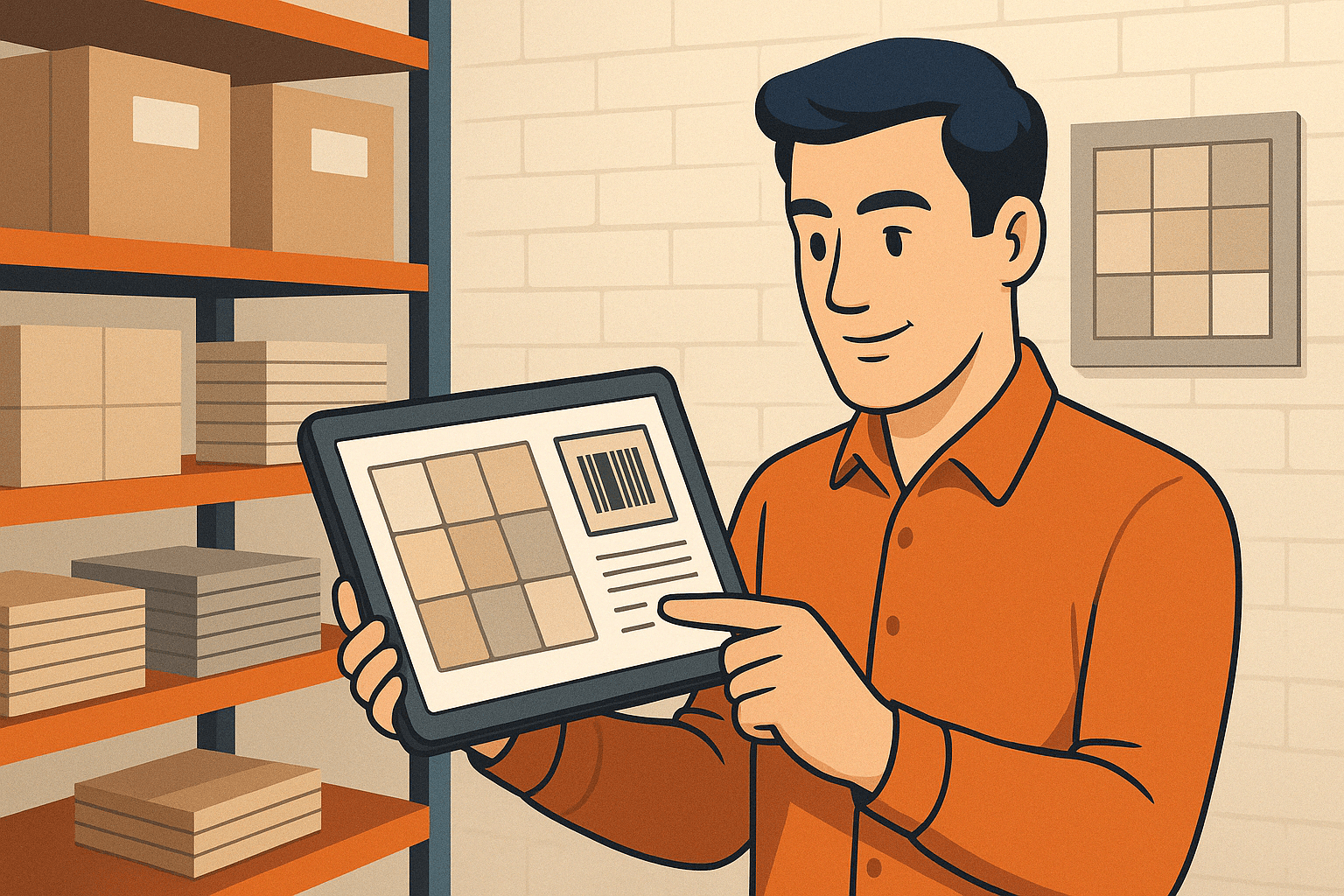
The Importance of Dye Lot Tracking for Canadian Tile Shops (And How Software Helps)
For Canadian tile shops and flooring suppliers, managing inventory goes beyond simply counting boxes. Tiles, especially ceramic and porcelain, are produced in batches, and slight variations in color, shade, or size can occur between these production runs. These variations are known as "dye lots." Failing to track and manage dye lots accurately can lead to significant problems, from mismatched installations to costly returns and damaged customer relationships.
What is a Dye Lot and Why Does it Matter?
A dye lot is essentially a batch number assigned to tiles produced under the same manufacturing conditions at the same time. While manufacturers strive for consistency, minor differences in raw materials, firing temperatures, or glazing processes can result in subtle variations from one lot to the next.
Why is this critical for tile shops?
- Color Consistency: The most noticeable issue is color variation. Installing tiles from different dye lots in the same area can result in visible shade differences, ruining the aesthetic of a project.
- Size and Caliber: Slight variations in tile size (caliber) can also occur, making installation difficult and affecting grout lines if not managed.
- Customer Satisfaction: Mismatched tiles lead to unhappy customers, complaints, and the need for costly rework or returns.
- Inventory Management: Without tracking, you might unknowingly mix lots in your warehouse or sell from different lots for the same order.
The Challenges of Manual Dye Lot Tracking
Attempting to track dye lots manually using spreadsheets or physical tags is incredibly difficult and prone to error, especially with large and diverse inventory:
High Risk of Error
Manually recording and verifying dye lots for every incoming shipment and outgoing order is tedious and increases the chance of mistakes.
Difficulty Preventing Mixing
It's hard to ensure that tiles picked for a single order all come from the same dye lot when relying on manual processes.
Time-Consuming Searches
Finding specific dye lots for add-on orders or replacements can be a time-consuming manual search through inventory records.
Lack of Visibility
Without a centralized system, it's difficult to get a quick overview of which dye lots you have in stock and in what quantities.
How Inventory Software Solves Dye Lot Tracking
Dedicated inventory management software designed for the flooring or construction materials industry provides essential features for seamless dye lot tracking:
1. Lot Number Tracking
The software allows you to record and track inventory by specific dye lot numbers from the moment it's received.
2. Inventory Segmentation by Lot
Inventory is automatically segmented and managed based on dye lot. You know exactly how many tiles of a specific product you have for each individual lot.
3. Picking and Allocation by Lot
When creating a sales order, the software allows you to specify or automatically allocate inventory from a single dye lot. Some systems can even prevent you from mixing lots on an order.
4. Historical Tracking
Easily look up which dye lot was sold to a specific customer on a previous order, which is invaluable for managing add-on orders or addressing issues.
5. Reporting and Visibility
Generate reports on inventory levels by dye lot, track the movement of specific lots, and gain clear visibility into your dye lot inventory.
6. Quality Control Integration
Some advanced systems may allow linking quality control notes or images to specific dye lots.
Conclusion
For Canadian tile shops, accurate dye lot tracking is not just a best practice; it's a necessity for ensuring quality, minimizing returns, and maintaining customer trust. By leveraging inventory management software with robust dye lot tracking capabilities, you can eliminate manual errors, streamline your operations, and confidently manage your tile inventory with precision.
Interested in improving your dye lot tracking? Learn how InterSource can help.
InterSource Team
Content Specialist
Construction industry expert with over 10 years of experience in inventory management and supply chain optimization.